In the highly regulated world of chemical manufacturing, building or renovating a laboratory requires careful planning to ensure both safety and cost-effectiveness. Chemical manufacturers face the challenge of balancing budget constraints with the need for compliance, functionality, and safety in their lab environments. In this guide, we explore key cost-saving techniques for lab construction that do not compromise on quality or regulatory requirements.
1. Optimize Lab Design for Efficiency
One of the most impactful ways to reduce costs in lab construction is by designing a functional and efficient layout. A well-thought-out design can minimize the amount of space needed, reduce the number of materials used, and improve workflow. Key strategies include:
- Modular Design: Using pre-fabricated or modular components can speed up construction time and reduce labor costs.
- Space Efficiency: Optimize the use of space to avoid unnecessary construction and utility costs. Combining workspaces for similar activities can eliminate the need for redundant rooms or equipment.
- Flexible Layouts: Design the lab to be adaptable for future changes or expansions, which avoids costly renovations later.
2. Implement Value Engineering
Value engineering focuses on identifying ways to reduce costs without compromising on essential lab functionality. This involves:
- Material Substitution: Use cost-effective materials that still meet the necessary safety and durability standards. For example, non-corrosive metals or alternative finishes can reduce long-term maintenance costs.
- System Integration: Where possible, integrate systems like HVAC, fume hoods, and electricals to reduce duplication and optimize energy efficiency.
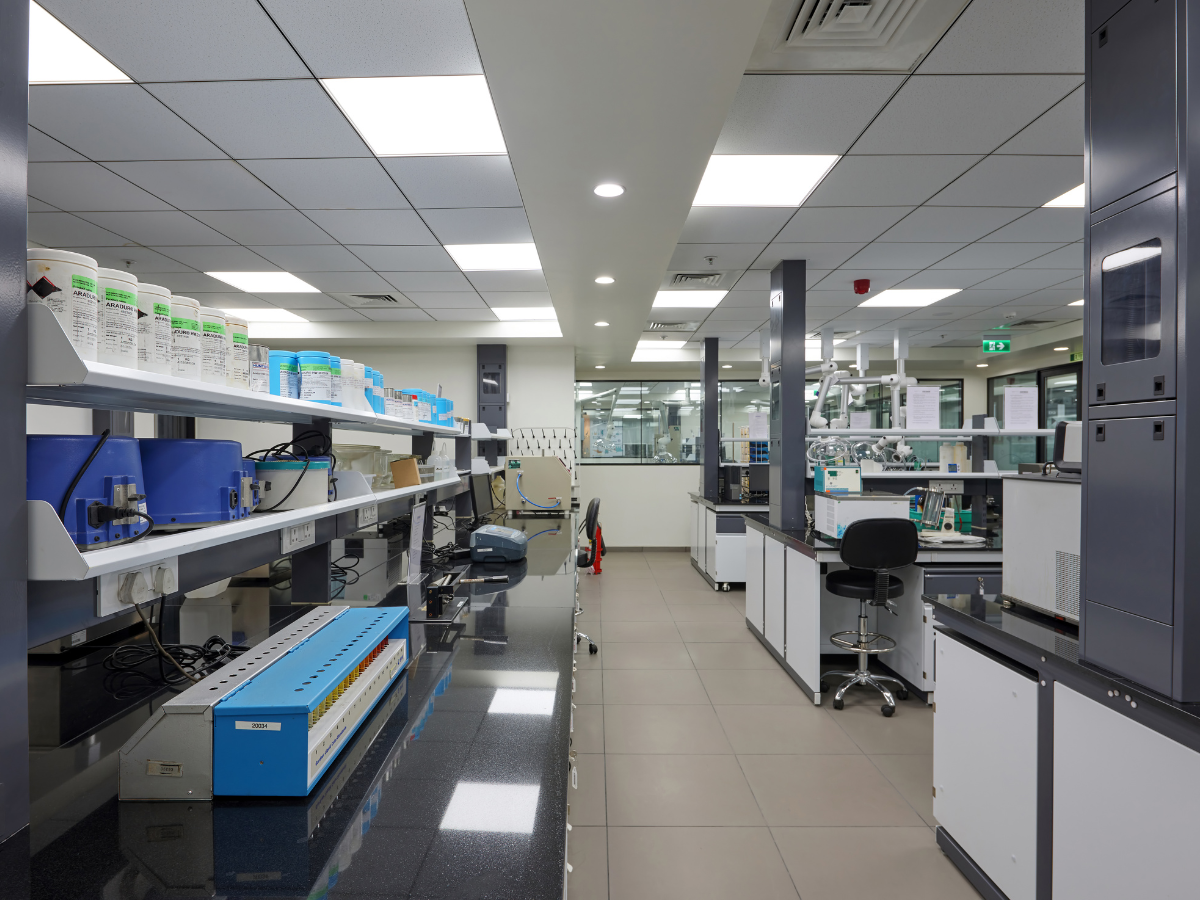
3. Use Pre-Engineered Lab Equipment and Furnishings
Choosing pre-engineered lab equipment and furnishings instead of custom-built solutions can result in significant savings. Prefabricated furniture, storage units, and modular systems not only reduce initial costs but also provide flexibility for future reconfigurations.
- Pre-fabricated Fume Hoods: Ready-made fume hoods and laboratory enclosures can be installed quickly, reducing labor costs and construction time.
- Standardized Lab Furniture: Off-the-shelf lab furniture such as benches, shelves, and cabinets can save on custom design and manufacturing costs.
4. Leverage Energy-Efficient Solutions
In chemical manufacturing labs, energy costs can be one of the largest ongoing expenses. Energy-efficient solutions can reduce both construction and long-term operating costs:
- LED Lighting: Installing energy-efficient LED lighting systems throughout the lab.
- High-Efficiency HVAC Systems: Use HVAC systems designed for energy efficiency, which also improves air quality and reduces maintenance needs.
- Building Insulation: Proper insulation helps control temperature and humidity, reducing energy demands on the lab’s climate control systems.
5. Streamline Procurement and Use Transparent Pricing
Transparent procurement processes can help identify the best pricing and minimize budget overruns. Ensuring a clear breakdown of costs and timelines helps avoid surprises during the project:
-
Detailed Cost Estimates:
Obtain detailed cost estimates for materials, labor, and time. This ensures all stakeholders are on the same page regarding costs and expectations.
-
Competitive Bidding:
Solicit bids from multiple contractors and suppliers to ensure competitive pricing and find cost-effective solutions.
-
Long-Term Supplier Relationships:
Establishing long-term relationships with suppliers can lead to discounts, better terms, and priority service.
6. Outsource Project Management for Efficiency
Hiring a skilled project management team or using a turnkey contractor can streamline your lab construction process, reducing delays, waste, and unforeseen costs:
-
Experienced Project Managers:
Skilled project managers can keep the project on track, manage budgets, and ensure compliance with safety and regulatory standards.
-
Turnkey Solutions:
Using a single contractor to handle design, construction, and equipment procurement minimizes miscommunication and the need for multiple subcontractors.
7. Plan for Future Scalability
Designing labs with scalability in mind can prevent expensive future expansions. A scalable lab design ensures that future upgrades and expansions can be carried out with minimal disruption or additional construction costs. Consider including:
- Modular Walls and Utilities: Plan for future expansion by using modular walls and utilities that can be easily upgraded.
- Space for Additional Equipment: Design the lab with enough space for future equipment without requiring costly renovations.
Conclusion
ScienceByDesign (SbyD) delivers cost-effective lab construction solutions for chemical manufacturers by utilizing modular designs, value engineering, and energy-efficient technologies. Our transparent pricing ensures no hidden costs, while our experienced project management team ensures projects are completed on time and within budget. SbyD helps you build efficient, scalable labs that meet all safety and regulatory standards, reducing long-term costs and supporting your operational success.